North American Stainless Seeing Benefits From Use of AI to Help Make Steel
The Kentucky-based supplier is rolling out AI in a company-wide digitization process showing promising results, such as in electricity savings
By John P. Desmond, Editor, AI in Business
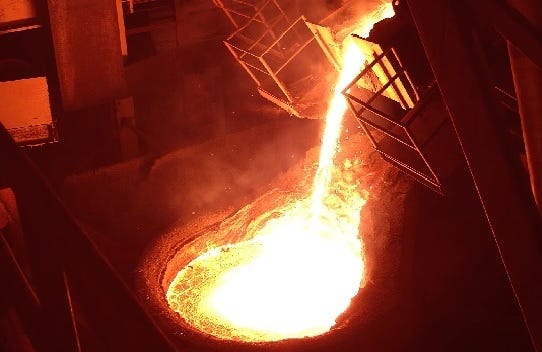
North American Stainless (NAS), one of the biggest suppliers of stainless steel in the world, is incorporating AI into its digitalization efforts, with encouraging early results in helping the company to gain efficiencies.
“We’re looking at AI to help us make stainless steel, and we face three challenges,” said Everett Vazzana, Digitalization Manager with NAS, speaking at the MIT MIMO and MIT CSail Symposium held this week on the MIT campus. Leaders in the manufacturing industry joined with related MIT faculty to discuss how AI is having an impact on their businesses.
Founded in 1990 in Kentucky, NAS runs a state-of-the-art production facility on 1,400 acres with direct access to the Ohio River, whose water is needed to help cool the steel reaching temperatures of over 1,500 degrees Celsius (2,732 degrees Fahrenheit) as it is processed.
The three challenges identified by Vazzana included: data, horizontal application of use case data and managing expectations.
On the data challenge, Vazzano said, “Merging the traditional system with AI and machine learning is a hot topic.”
On the second challenge, Vazzana noted that use cases are developed for a specific process, which is extremely customized. “We can’t take a tuned model from one use case and apply it to another,” he said.
Managing expectations for AI is a double-edged sword. The general awareness of how AI is having an impact in everyday experience, especially with the emergence of ChatGPT into the mainstream, is causing more people to assume that AI can do it all. “They ask, ‘why isn’t AI running the plant now?’ “ Vazzana said.
Vazzana relayed a personal experience to explain how his interest in technical work arose. He was at a robotics exhibition in Pittsburgh as a child, when he saw a pogo stick robot and was struck. “It was tethered, but still very impressive,” he recalled. It got him interested in pursuing electrical engineering and manufacturing as fields of study. He has worked at the NAS plant for over 25 years now, so has relationships with workers throughout the plant.
These relationships have proved pivotal as Vazzana has worked to infuse AI into plant operations. “For data science, you need an extremely diverse team,” he said, mentioning machine learning, data visualization, programming, statistics, software engineering and data pre-processing as among the desired skill sets.
Another experience set that might surprise some about being true of a manufacturing plant, is ethics. “Many ethical decisions come up when we look at data, because data is power,” Vazzana said, using vision safety systems as an example. He treads carefully around potential changes to the culture of the plant that can sometimes risk negative consequences.
The plant manufacturing process includes a melt shop, a hot mill, a cold mill and finishing, that in the end produce bars of steel or rolls of thinner stainless steel. “We’re not making a first-user product,” he said, but rather supplying raw materials to other manufacturers.
The NAS Digitization effort that Vazzana works on includes a staff of six people. “We’re a little stressed out,” he said of the workload. He described the digitalization technology stack, needed to process over 30,000 data signals from all the systems each day. Dashboards monitoring the plant feature histograms, flow charts and heat maps.
Vazzana described work on the Electric Arc Furnace power optimization project, designed to help save on electricity costs. “We produced a model to optimize the stainless steel melting process, using very advanced analytics,” he said. “If we can use less electricity to produce steel, it will help with our carbon footprint.”
The model is measuring 20 features of the new system performance compared to benchmarks. The results have been very encouraging so far, with data distribution results displayed in a bell curve graph. “We tightened up the curve, which resulted in a two to three percent benefit in kilowatt-hours,” he said, a significant impact since the EAF is using 50 percent of the electricity needed to run the plant.
The goal of a second use case he presented, called Generalized Signal Modeling, was to use a cloud-based ML system to bring insight into the volumes of data signals being generated daily. “The idea is if you have an issue on a part of a machine, you should be able to see it,” such as with yellow, red and blue colors on a heat map. An example issue would be low air pressure in a banding machine, or a decrease in cooling water flow to a material processing sensor.
NAS is working with Falkonry, a Cupertino, Calif.-based company founded in 2013 that offers time series AI products aimed at helping digital transformation, especially for manufacturers. “Falkonry can discover insights hidden in your operational data and deliver timely, actionable intelligence,” the company’s website states.
Falkonry has clients in the manufacturing and defense industries, having won contracts with the US Navy Office of Naval Research, for example, to deploy its Digital Insights products in ships on the high seas. The product can detect every sensor data point to identify reliability and performance anomalies, an analysis that helps operations teams determine root causes.
In a press release issued by Falkonry on the Navy contract, Founder and CEO Nikunj Mehta stated, ”We have seen demand for increased AI computing in the field, especially to leverage operations data for higher operational and personnel productivity.”
Another recent press release announces the recent availability of an AI co-pilot based on years of collaboration with customers in the metal and energy industries. These industries are generating large quantities of time series data, which is among the fastest growing types of data in the world. “We have seen a major shift from yesterday’s AI systems that monitor the health of a few assets to a Generative AI-powered plant-scale system for continuous productivity improvement using massive data from different sources across the plant,” stated CEO Mehta.
Vazzana said of the potential for AI to help NAS, “We’re excited about this,” emphasizing the company is still implementing the new solutions. Other use cases that have potential benefits include vision systems, logistics, safety and natural language processing.
While he sees progress, Vazzana knows there is a way to go. “In manufacturing, we’re still tethered to the pogo stick,” he said.
Read the source information in a press release issued by Falkonry on its Navy contract, and in a press release on a new AI co-pilot project.
(Write to the editor here; tell him what topics you would like to read about in this newsletter.)